If you work with rotating equipment, you understand the importance of proper alignment and balance.
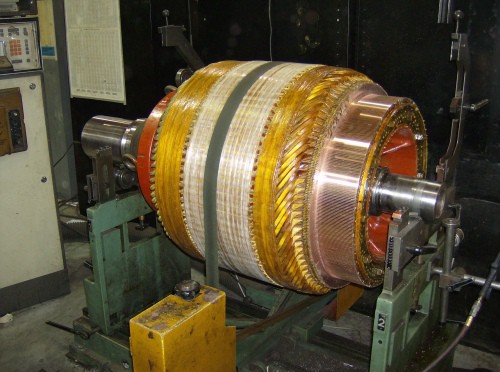
Improper dynamic balance, which is the most frequent type of balance problem, can cause excessive vibration that can lead to extensive machine damage.
Such devastating system failures can easily lead to troublesome downtime and massive repair or replacement costs. Machines with rotating components must be tested and measured in order to ensure accuracy. The process of dynamic balancing measures any existing imbalance in these components. Through the use of advanced electronic equipment, experts can pinpoint and measure imbalances to identify the cause.
Detected imbalances can often be corrected very simply, often by merely adding or subtracting weight from the imbalanced area of the rotating part. Experts will then monitor the part closely to determine whether the vibration has been reduced to acceptable levels.
Overview of Dynamic Balancing
Rotors may possess any number of imbalances randomly distributed throughout the part’s rotational axis. Dynamic balancing is the process used to correct these random imperfections that cause the unbalance. A component must be rotating in order to effectively measure its level of unbalance.
Dynamic unbalance is correctable only by achieving balance between these two planes:
- Two-plane unbalance is caused when the distribution of mass in the rotor is out of sync with the rotational axis.
- While the rotor spins rapidly about its axis, experts can utilize sensitive and specialized electronic equipment in order to measure any present balance issues.
- Once the cause of the vibration/imbalance is identified, the center mass of the rotor can be balanced in line with the axis of rotation to eliminate the problem.
Benefits of Dynamic Balancing
Dynamic balancing of rotary equipment offers numerous benefits, such as:
- Vibration control. Vibration is caused by unbalanced rotation and is often a source of difficulty and damage for equipment with rotating components. The dynamic balancing process significantly reduces vibration and consequently extends the lifespan of components and machinery.
- Vibration also produces noise pollution. Operator fatigue and safety can be addressed in part through dynamic balancing. Many operators experience a decrease in efficiency after prolonged exposure to high levels of vibration and noise. When those factors are eradicated, operators can perform their duties more effectively. Operator safety also increases due to the reduced rate of machine failure.
- Service life. Dynamic balancing solves some of the issues surrounding stress and component lifespan. Rotating components, bearings, and surrounding equipment experience longer service life when appropriately balanced.
- Operating costs. Many operations must keep extra equipment on hand so that production can continue in the event of a breakdown. By using reliably balanced rotors, the need for this back-up equipment can be significantly reduced.
Dynamic Balancing from Renown Electric
For over 40 years, Renown Electric has provided our customers with advanced dynamic balancing services in our own facilities as well as in the field. We employ state-of-the-art methods and equipment—like the VIBXPERT II state-of-the-art balancing system.
Dynamic balancing allows us to measure and calibrate your rotating equipment before imbalances can cause any major problems; it is important to remember that correct balance and alignment is ideal for improving the performance and extending the life of your rotating equipment.
Since Renown is an ISO 9001:2015 registered company, you can be assured that our dynamic balancing services offer the highest levels of quality and reliability.
To learn more about the benefits of Renown’s dynamic balancing services and our overall preventative and predictive maintenance program, please contact us today.
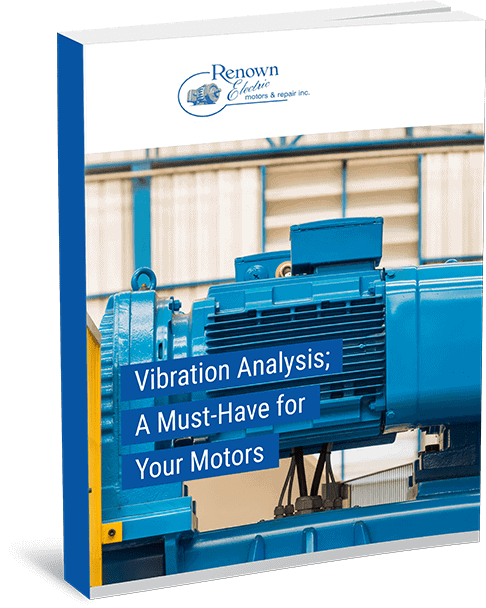
Vibration Analysis: A Must-Have for Your Motors
Vibration Analysis is a time-tested diagnostic tool that quickly and effectively identifies faulty components and problem areas in facility equipment from mechanical problems. Download our eBook to learn more.
Download Your CopyDynamic Balancing Solutions
Rely on us for dynamic balancing as a part of our custom preventive and predictive maintenance program to diagnose and resolve problems before they lead to costly system failures.
Contact Us