Overview of the Aggregate Industry
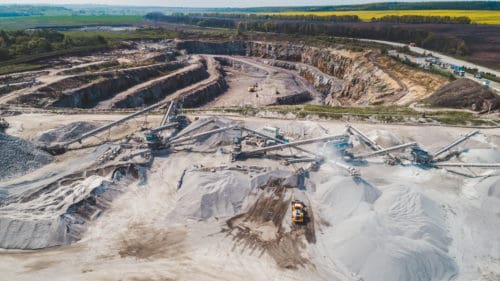
The modern world as we know it would not exist without aggregate. Aggregate refers to the raw material used for construction (e.g., stone, sand, and gravel). Once it is mined, washed, processed, and/or combined with a binding medium and other important compounds, it can be used to create building materials for roads, bridges, buildings, and other structures critical to our present society.
Electric motors play an essential role in aggregate mining, processing, and handling operations. Since aggregate is so vital to our day-to-day lives, it is important to keep these machines properly maintained and repaired. Otherwise, we risk an aggregate shortage, which puts many critical construction projects at risk.
Importance of Generator and Motor Maintenance and Repair for the Aggregate Industry
In the aggregate industry, motors are used to power a variety of equipment, such as crushers, hoists, and pumps. While the industry’s applications generally demand reliable and durable machinery, the harsh conditions commonly found within them often negatively impact equipment performance if a proper servicing plan is not established and followed.
The failure of a motor means a stop in production, which results in extended timelines and reduced profit margins. As such, it is important to address any motor issues that arise immediately (e.g., repair or replace worn components) before they can lead to failure or other significant problems. Regular inspection and appropriate repair can lead to greater uptime and savings for a facility.
Partner With Renown Electric for Electric Motor Maintenance and Repair Needs
Renown Electric has provided electric motors and electric motor repair for nearly four decades. We offer our products and services to customers across a wide range of industries, including the aggregate industry.
Our team is fully aware that the failure of a motor can mean significant losses for an aggregate industry facility. That’s why we are committed to providing quick, cost-effective, and quality maintenance and repair solutions. Equipped with highly skilled technicians, computerized testing processes, and modernized repair equipment, we can serve as a one-stop shop for all electric motor management needs.
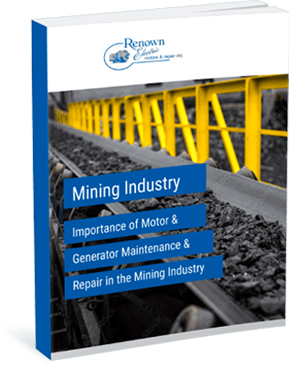
Together, We'll Keep Your Aggregate Operations Running!
Mining Industry, Aggregate & Battery Electric Vehicle (BEV) markets rely upon motors & generators heavily to meet high production demands in rugged environments. Download our eBook to learn more about proper maintenance to provide longevity and durability.
DOWNLOAD EBOOK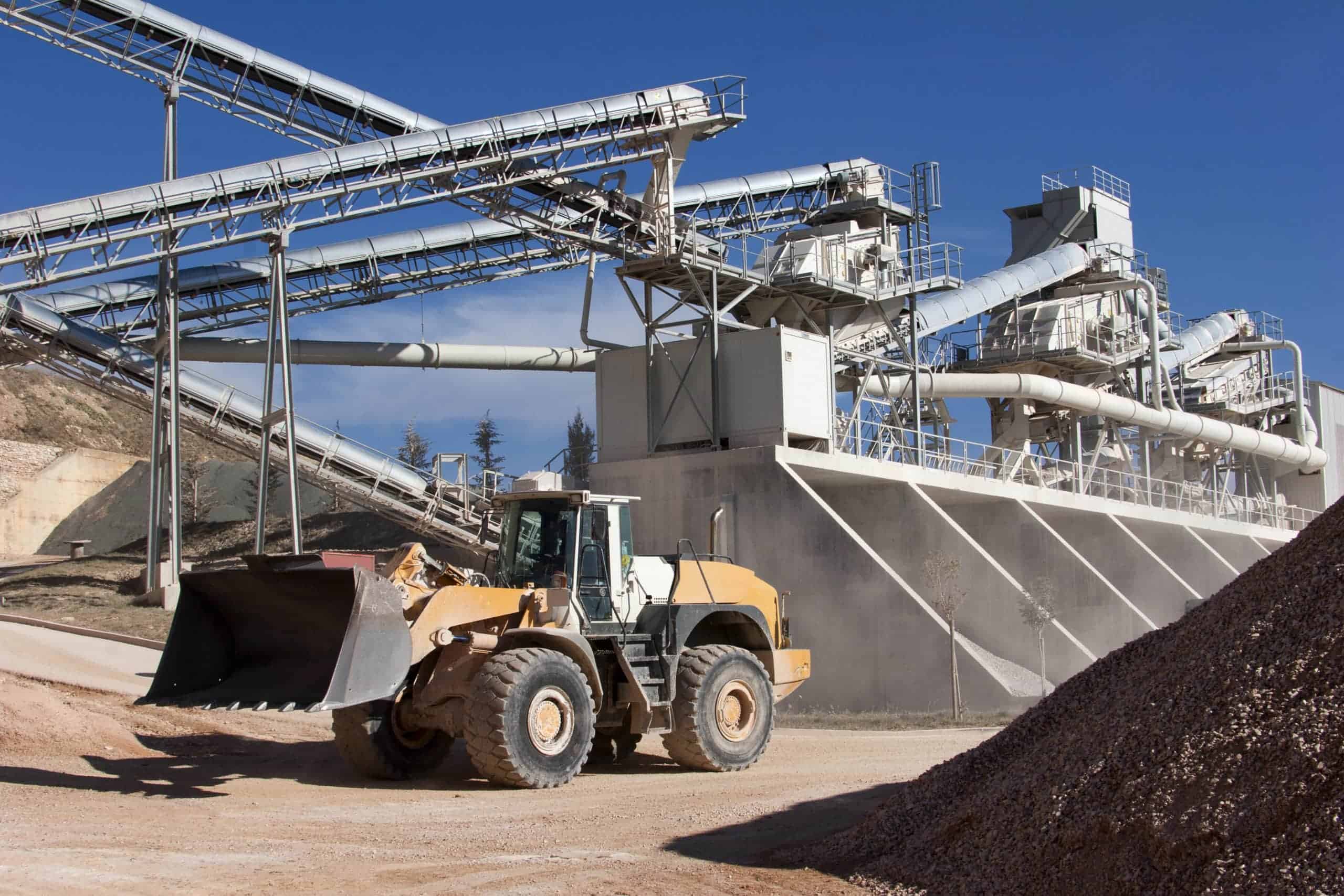
Our service offerings include:
- Generator rebuilding & rewinding
- Machine shop services
- Motor drive (VFD) repair
- Motor rebuilding & rewinding
- Preventative maintenance
- Pump repair
- Servo motor repair
- Sheave regrooving & manufacturing
As a CSA qualified and ISO 9001:2015 certified company, we can provide an electric motor management solution that meets or exceeds your specifications and standards. To learn more about our electric motor maintenance and repair services, contact us today.
Common Electric Motor Maintenance and Repair Operations in the Aggregate Industry
Electric motor maintenance and repair operations can vary from industry to industry and facility to facility. In the aggregate industry, typical operations used to increase the reliability and longevity of electric motors include:
Bearing Analysis and Repair
Bearing problems are the most common cause of motor failure. Typical issues include wear, too much/too little lubrication, and improper fit or installation; they can cause a bearing to emit excessive vibrations.
If a motor has a potential bearing problem, a maintenance professional can help determine the source and offer an appropriate solution. Solutions include rotating the motors, properly installing a correctly sized bearing, and adding/removing lubrication.
Motor Balancing
Unbalanced motors generate excessive noises and vibrations upon startup. As the motor operation speeds up, the noise and vibration will also increase. If balancing issues are not handled quickly, they can lead to premature bearing wear, structural damage, and, in the worst-case scenario, equipment failure.
One solution for an unbalanced motor is sending the unit back to the manufacturer. However, on-site dynamic balancing offers numerous advantages. For example, it has shorter lead times and lower service costs.
Motor Drive Alignment
Misalignment refers to when the motor shaft and the connected system (e.g., generator, gearbox or pump) are not properly aligned. It can lead to a variety of problems, such as excessive and premature wear on bearings and belt drives and unnecessary friction on shafts. These effects can lead to increased downtime, reduced productivity, and decreased safety.
Laser measuring equipment enables motor servicing professionals to quickly and easily check the alignment of motor drives. If misalignment is detected, they can adjust the motor or driven equipment as needed.
Vibration Analysis
Motors naturally generate vibrations. Motor servicing professionals use vibration analysis to determine whether the vibrations a unit is producing are normal or excessive. In the case of the latter, they may conclude there is a problem. Typical problems associated with excessive vibrations include bearing failure, imbalanced motor, poor power quality, bad VFD or misaligned drive. Traditional vibration analysis can be combined with RDI Motion Analysis which can show structural issues that contribute to vibration in the system as well.
Winding Analysis
An electrical motor winding analysis can detect future problems in electrical components before they occur. It can be used for alternating current (AC), direct current (DC), and synchronous motors. A comprehensive winding analysis program can provide some insight into the health of the electric motors insulation system which is a good predictor to determine longevity of the motor system.
Keep Your Mining Motors & Generators Running Smoothly!
To learn more about our electric motor maintenance and repair services or discuss your service requirements with one of our team members, contact us today. Our 24/7 customer services ensure we can help extend the performance and life of your electric motors when you need it.
Let's Discuss Your Project