Introduction to Motor Winding Analysis (MWA)
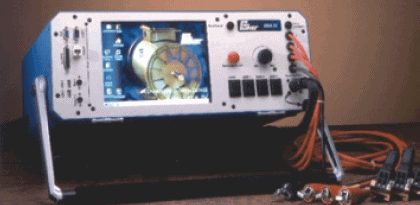
A crucial aspect of preventative maintenance in electric motors and generators is estimating the remaining lifespan of the insulation system of rotating equipment. That information can be compared with different operating conditions — pertaining to load, cycling, or the environment — to assess how and when the motor will be affected. To detect and resolve motor issues preemptively, Renown Electric Motors & Repair Inc. utilizes electric motor winding analysis (MWA).
What Is Electric Motor Winding Analysis (MWA)?
With electric motor and generator winding analysis, our skilled technicians can discover early-stage problems inside rotating electrical equipment before they become more substantial. This early detection method allows us to perform the appropriate repairs during planned downtime. In addition to reducing repair costs during unscheduled shutdowns, winding analysis can lessen costs associated with disastrous component failure. Winding analysis is a form of non-destructive testing (NDT) that can be used for motor, transformer, and generator windings.
Alongside MWA, current signature analysis helps classify electric winding insulation. This information helps us detect any problems associated with premature component failure, which, in turn, prevents the loss of production time and high maintenance costs.
Winding failure analysis upon inspection of a failed unit is an ideal method for diagnosing system-related issues that affect the winding. In addition to active winding analysis for monitoring the dielectric strength of your winding insulation in-situ, the combination of methods forms a necessary aspect of any electric motor or generator preventative maintenance plan.
Main Benefits
MWA is an advantageous diagnostic measure for large electric motors and generators. Some of the primary benefits of checking motor windings periodically and proactively include:
- Finding problems early on to avoid catastrophic motor or generator failure. If left unchecked, small issues like general wear in your insulation will become larger. By identifying the existence of wear or damage early, you can safeguard against equipment failure, unplanned shutdowns, lost time and profits, and costly repairs. Preventive maintenance also allows you to schedule any necessary repairs during planned system downtime for greater efficiency.
- Improving safety in your operations. Not only will failing systems prove disastrous for productivity and your bottom line, but malfunctioning motors and generators can pose a safety risk to your facility and workers. Ensuring that winding systems are functioning properly limits the chance of such hazards.
- Supporting peak performance, efficiency, and reliability in your motors and generators. Even well-cared-for insulation will experience degradation over time. Additionally, motor windings may become unbalanced, diminishing the performance of your equipment. Proactive analysis helps keep your motors and generators running smoothly for reliable functionality whenever you need them. Doing so also boosts efficiency and reduces energy use and costs.
- Saving on expenditures. Speaking of costs, as a preventive maintenance method, MWA allows you to deal with maintenance issues as they occur, which is much more cost-effective. Failing to make repairs as problems arise or waiting to replace parts until they fail can be a very expensive mistake, as these problems will worsen and potentially affect other components.
- Ensuring regulatory compliance. Routine motor winding analysis will help make sure that your equipment adheres to all necessary, current industry regulations and standards regarding functionality and safe operations.
- Maximizing equipment longevity. Preventive maintenance keeps integral — and expensive — motors and generators in optimal running condition, encouraging peak performance and leading to a longer lifespan and improved ROI. Better quality assurance is also possible, all while utilizing a non-destructive testing method that won’t harm your equipment.
- Developing maintenance services and scheduling that are specific to your needs. As you carry out periodic motor winding analyses and gather operating data on your specific equipment, you’ll then be able to develop an informed, custom preventative maintenance plan that optimizes efficiency.
Types of Motor Winding Insulation Tests
MWA is composed of three essential tests that ensure the efficacy of motor winding insulation, as follows:
- Electrom TIG 12-D. Using DC voltage, this nondestructive testing technique detects leaks, which it measures in micro-amps.
- On-line tests. Per phase as well as Rotor Bar tests, on-line testing assesses voltage and amperes.
- Off-line tests. Examples of off-line tests include the Surge Test, Hipot Test, and the One-Minute Megger Test.
Premium Electric Motor Winding Analysis Services From Renown
At Renown, we utilize the most state-of-the-art equipment for our motor winding analyses on every repair in-house or in the field, (for AC and DC motors & generators, respectively). If you can’t make it into our shop, don’t worry — our testing equipment can be pre-programmed and quickly brought to you in the field.
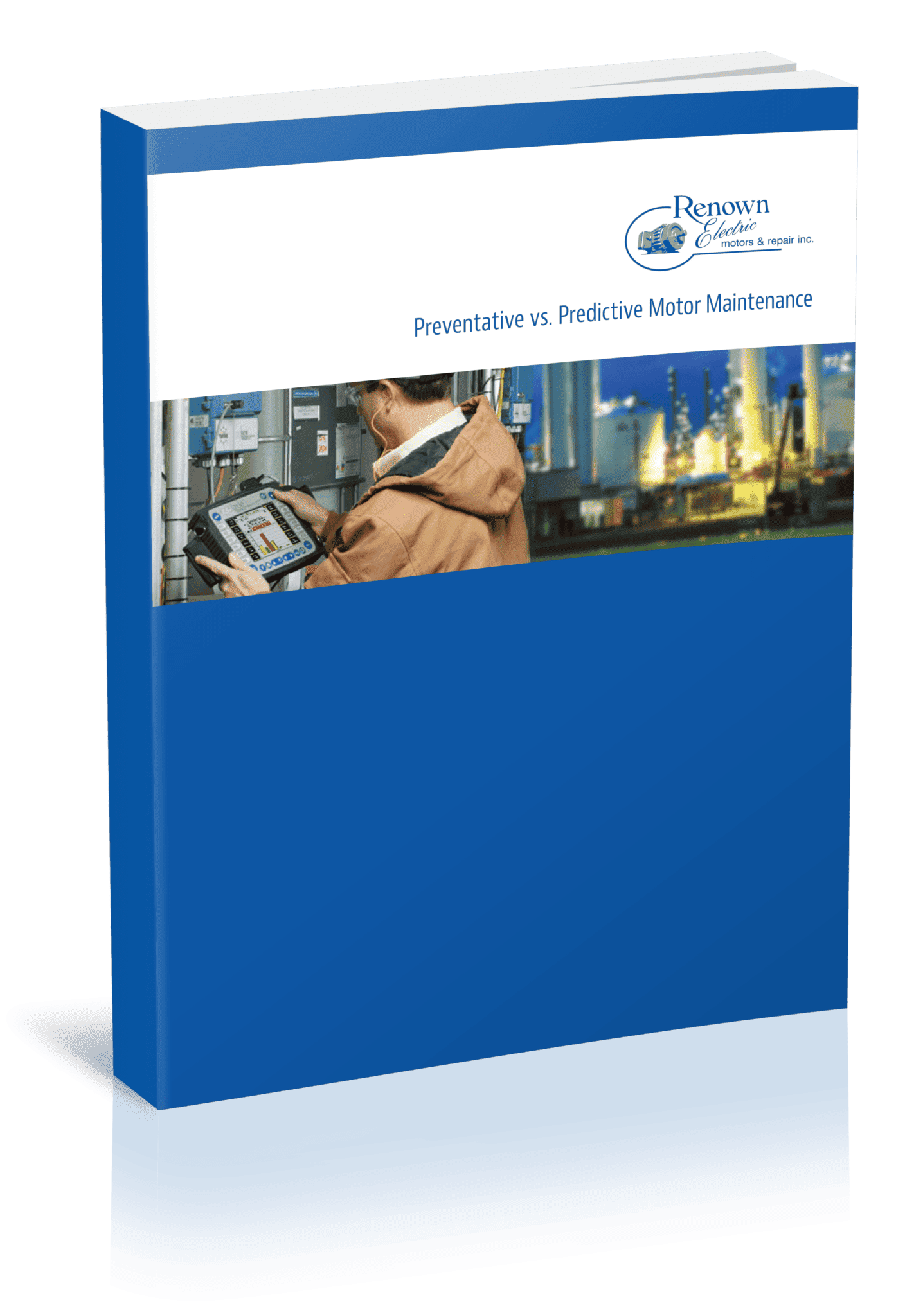
Preventative vs Predictive Maintenance
Let Renown Electric help you implement the right maintenance program - this is imperative, as it can greatly reduce costs and unplanned downtime.
Download eBookUncover Hidden Motor Issues
Prevent costly downtime and optimize performance with our expert analysis.
Contact Us