Reduce Inventory Costs & Better Organize Your Supply Chain
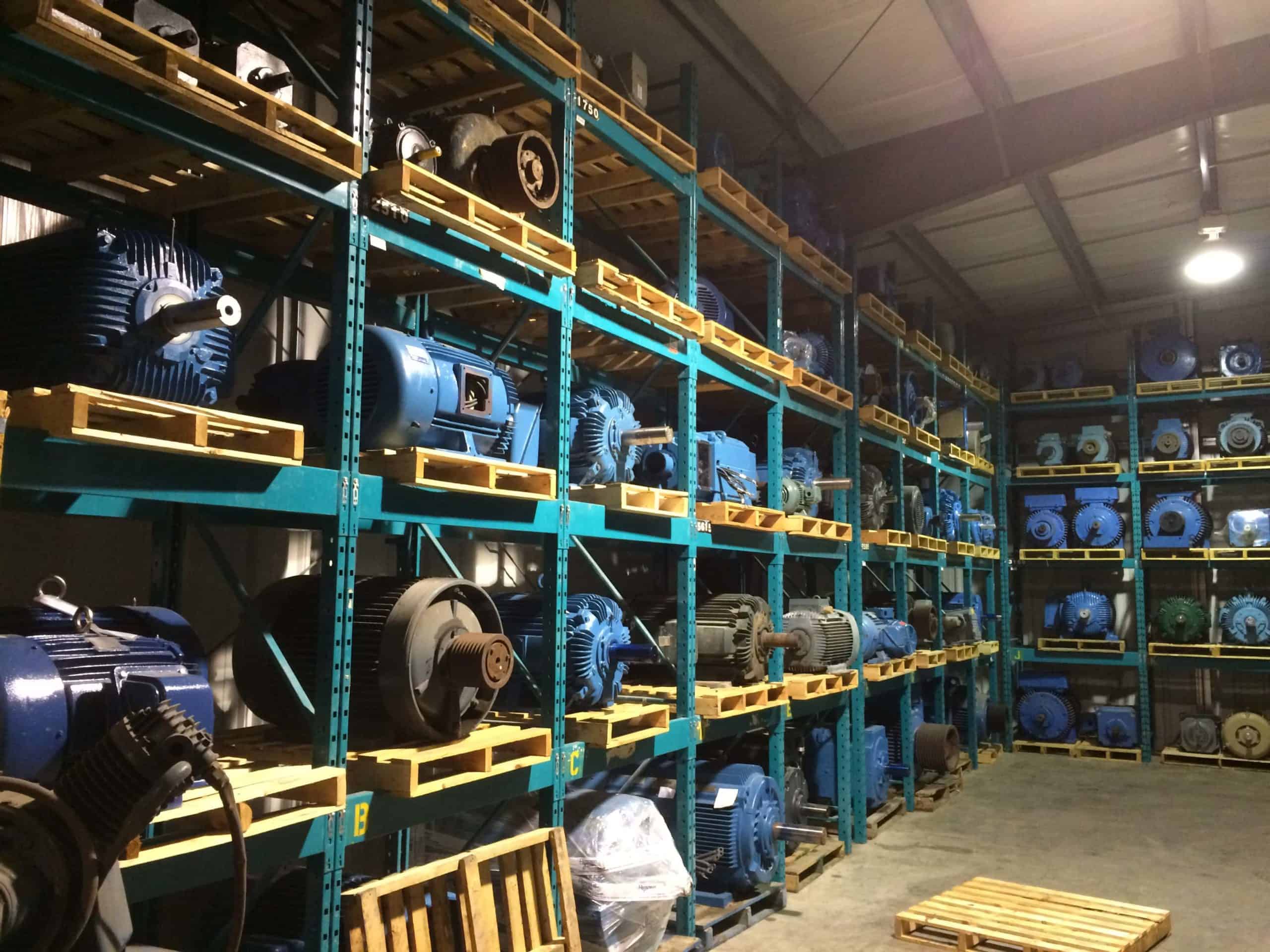
Renown Electric offers a motor management program that effectively reduces your inventory costs and better organizes your supply chain.
Our motor management team works with your personnel to conduct an inventory of all motors in the plant, both in and out of service. We’ll then determine what spares are needed and eliminate any excess inventory to free warehouse space and increase production efficiency.
How Renown Electric's Motor Management Program Works
Phase 1:
Physical “In-Plant” Inventory of Spare Motors: Renown Electric, in collaboration with the customer, will conduct an analysis of all motors in operation and spares stored in plant. Motors will be tagged and the motor I.D. tag will be affixed to the motor.
Critical List Determination: The customer will establish a list with assistance from Renown personnel. Each department will identify motors as critical, expedite or standard service. Some critical motors may be deemed to remain in the plant to avoid down time.
- Critical: Motors will be delivered within 3 hours of dispatch.
- Expedite: Motors will be delivered within 24 hours of dispatch.
- Standard: Motor requiring long lead time or small items.
Step 1: Analyze Inventory: Renown will conduct a survey based on data collected to determine adequate levels of inventory. This analysis is reviewed with the company’s personnel.
Step 2: Removal of Excess Motors: Pick up of excess storage motors will be coordinated with Renown Electric and the plant to allow for efficient transfer. All motors will be tagged, inventoried and stored at Renown Electric. A full list of all motors transferred to Renown Electric will be supplied to each department.
Step 3: Repetition of Existing Inventory: Renown Electric will cross reference motors received at our location and identified as critical, expedite or standard (colour coded tags, separate storage areas). Plant personnel will determine possible reduction of inventory by assessing duplicate motors. As well, we will analyze critical motors to determine if additional spares are required. All motors stored at Renown Electric will be inspected and recorded. A list will be forwarded to plant recommending actions (possible repairs or disposal of units that are beyond economical repair).
Step 4: Create Computer Report: The initial computer report will note the quantity of each type of motors (including beyond economical repairs). Your company will make a determination if these quantities are sufficient for their plant operation and disposal of motors not economically repairable.
Phase 2:
The motors picked up from your company will be cleaned, tested and repaired if necessary. The initial computer report will note motors that are un-economical to repair. With this report, the quantity of each motor will be noted. Your company will make the decision if these quantities are sufficient for their plant operation, and disposal of motors not economically repairable.
Dedicated Contact Information: To facilitate seamless communication, we will provide business phone numbers, pager numbers, and overnight delivery phone numbers upon program initiation. All supervisors on your team will receive a copy of this contact list for easy reference.
Online Motor Management Matrix: Select personnel from your company will have secure, online access to the Motor Management Matrix. This interactive tool provides real-time access to critical motor data, including specifications, location within your plant, and current availability of spare parts.
To minimize downtime for critical motors, we understand the importance of rapid response. To achieve a 3-hour delivery window for these motors, please provide the following information when placing a request:
- Caller Identification: The name of the person calling from the plant and their pager number.
- Location Details: The area of the plant and machine that the motor operates with.
- Motor Identification: I.D. number of the motor or relevant motor specifications.
- Purchase Order: To cover repairs of burned out motors, a purchase order (possibly a blanket) is required.
The motor that is in need of repair will be returned to Renown Electric when the spare is delivered to the plant. The burned out motor will then become the spare and returned to storage at Renown Electric.
Through this comprehensive Phase 2 program, Renown Electric strives to become a valuable partner in maintaining optimal equipment operation within your facility.
Benefits of Motor Management
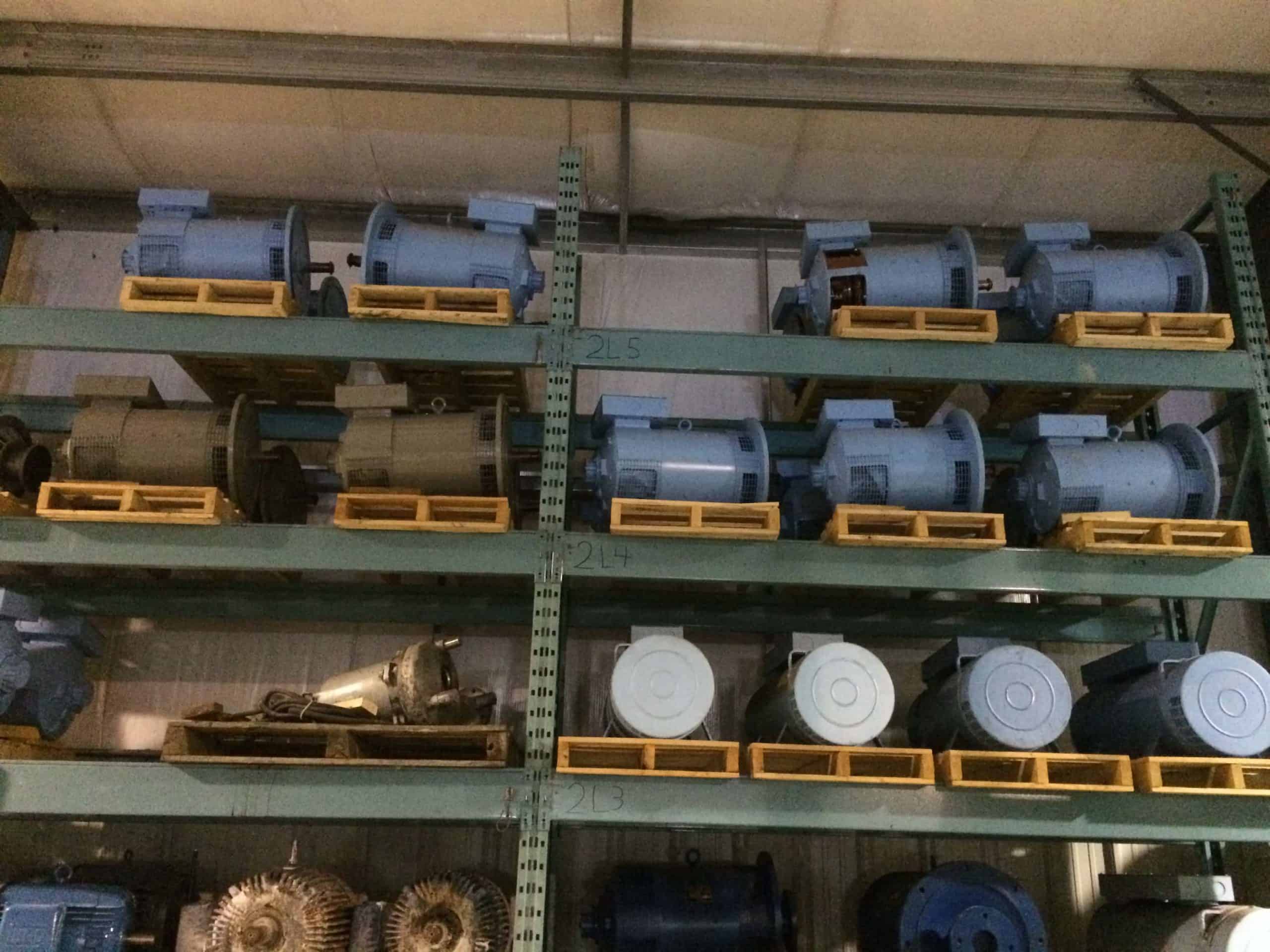
Proper motor management and storage can:
- Increase production efficiency
- Reduce costs of unscheduled downtime
- Eliminate unnecessary inventory build up
- Reduce costs associated with Electric Motors & Generators up keep
- Manage motors as an asset, rather than as a product
- Provide traceable historical motor data, including repair history, failure reports and motor efficiency, which will allow you to target problem motors and applications
- Effectively reduce inventory costs through an analysis in order to diminish duplication and disposal of obsolete or excess motors
- Complement a preventative or predictive maintenance program to reduce rewind costs by up to 70%
- Deliver documented energy efficiency savings and initiatives/grants
- Deliver proven savings at all levels of maintenance
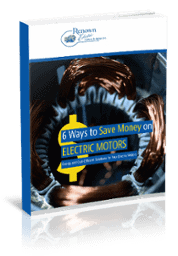
6 Ways to Save Money on Electric Motors
Renown Electric's skilled team leverages sophisticated technology and experience to keep motors running at top efficiency.
Download NowAdditional Field Services
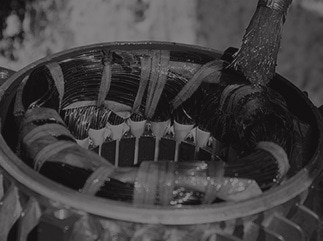
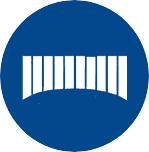
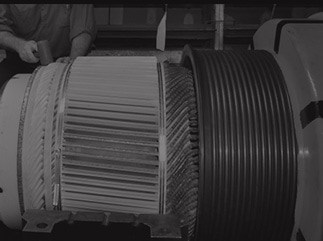
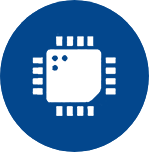
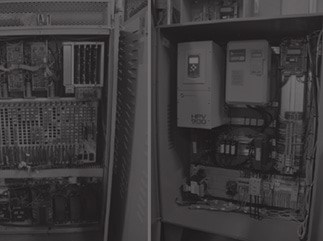
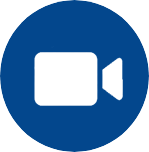
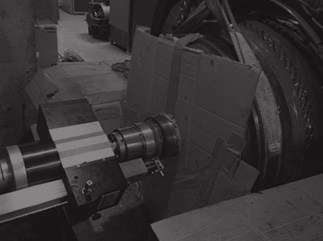
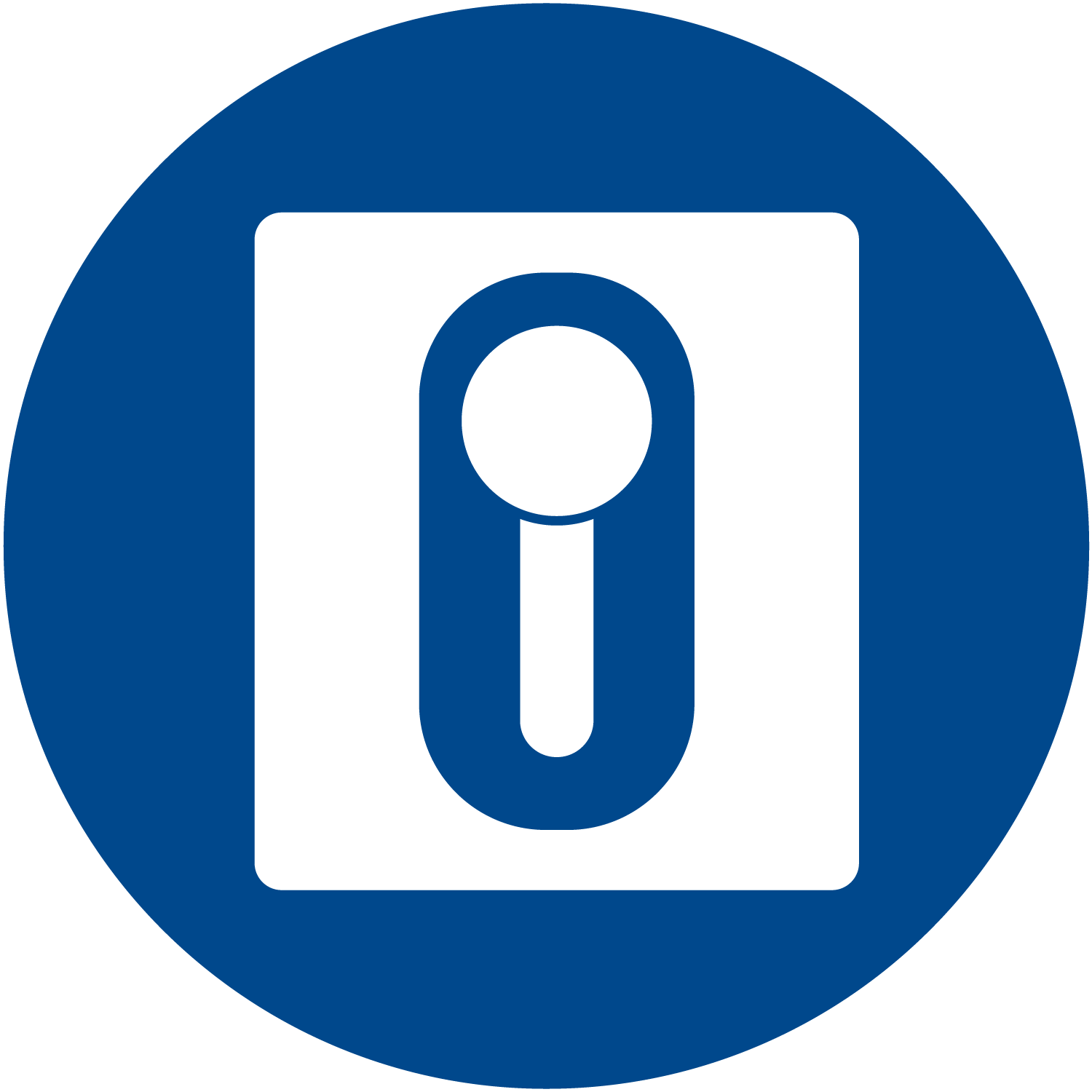
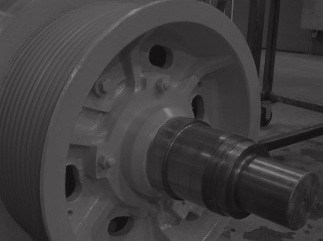
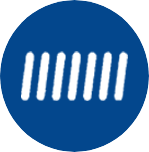
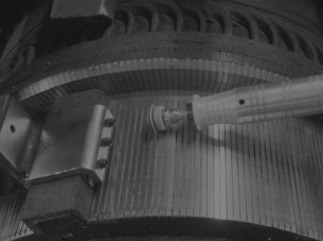
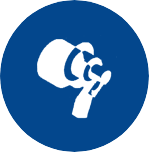
Get Organized Today!
A motor management plan ensures significant cost savings in both material and personnel. You’ll also minimize production downtime, streamline inventory, and have online access to your inventory 24/7.
Contact Us